In the metalworking sector, selecting production equipment is a strategic decision. It impacts flexibility, durability, and costs—key elements in optimizing every industrial process. This article, prepared by industry experts, aims to help you identify the most suitable tooling for precision cutting, customization, and production volume requirements.
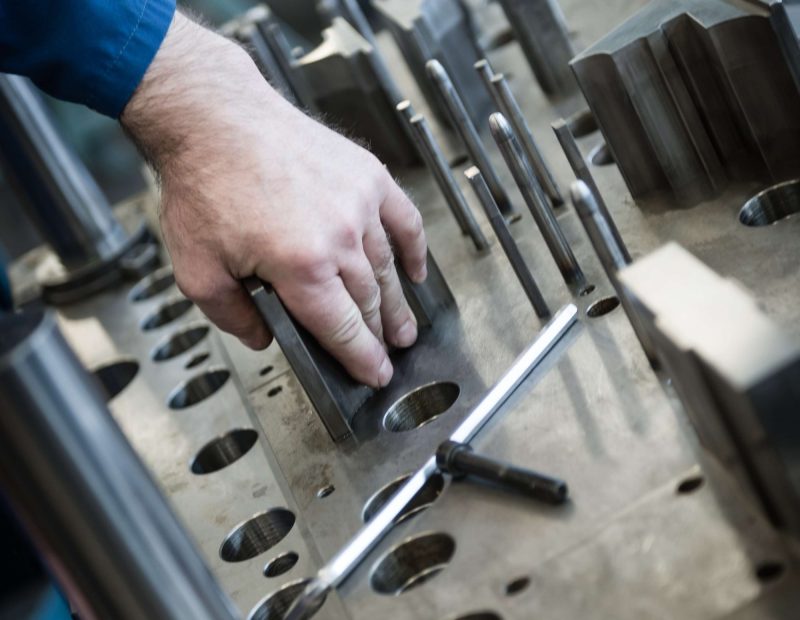
Part 1: Press Tools – The Ideal Solution for Large-Scale Production
1.1 Technical Features of Press Tools
Press tools provide optimal production capacity, especially for long production runs where consistency is critical, such as in the automotive industry. Every component must adhere to precise tolerances to fit seamlessly with other parts and ensure vehicle safety. Even deviations of a few tenths of a millimeter could compromise the integrity of the final piece.
For companies seeking a robust and reliable solution for large-scale production, Ouréval offers press tools designed to meet these demands. By automating production, Ouréval presses minimize manual quality checks and streamline inventory management, ensuring consistent uniformity throughout production.
1.2 Economies of Scale and Profitability
While the initial investment in press tools is significant, the return on investment (ROI) is often rapid for large-scale operations. For businesses producing over 100,000 units, economies of scale become significant, reducing unit costs, optimizing raw material use, and minimizing human errors.
Companies targeting a fast ROI benefit from increased profitability with these tools, as they help cut direct production costs and indirect costs related to storage and material waste. For example, a company using an automated press to produce 200,000 pieces annually can reduce per-unit costs by 60%, achieving ROI in under two years.
1.3 Industrial Applications
Press tools are indispensable in various industries, including:
- Automotive: Structural components like engine mounts, chassis parts, and body panels.
- Appliances: Heat-resistant parts such as stainless steel deflectors and resistance brackets.
- Construction: Metal structures and components for sustainable building projects.
1.4 ROI and Customized Analyses
For many industrial clients, ROI calculations are critical. For instance, manufacturers of safety components, such as locking mechanisms and fasteners, require total reliability for every piece. These demands justify the initial investment, demonstrating how press tools offer competitive advantages in quality and cost.
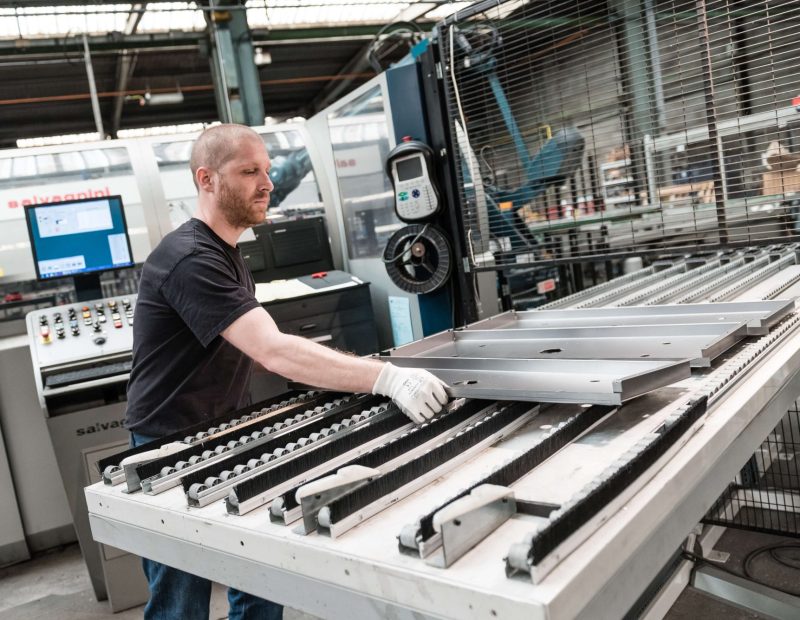
Part 2: Punching and Panel Bending Machines – Flexible Solutions for Diverse Projects
2.1 Punching Machines: Versatility for Customized Series
Punching machines enable diverse cuts without tool changes, making them a go-to solution for customized production. For example, in office furniture manufacturing, designs often need adjustments to meet client preferences. Punching machines provide this flexibility, delivering complex shapes without compromising production timelines.
2.2 Panel Bending Machines: For Thick Materials and Enhanced Durability
Perfect for handling thick materials, panel bending machines are highly valued in construction and heavy industries where metal structures must ensure maximum durability. This equipment offers precise bending capabilities, ideal for transport infrastructure or complex building frameworks.
2.3 Flexibility and Profitability for Medium-Scale Production
For small or medium-scale projects, punching and panel bending machines are cost-effective and flexible. In office furniture manufacturing, they enable the creation of custom designs without high tooling costs, ensuring quick adaptation and optimized flexibility for varying orders.
2.4 Adaptability to Personalization Trends
With growing demand for personalized products, punching machines offer manufacturers an economical option to meet custom order requests without slowing down production lines.
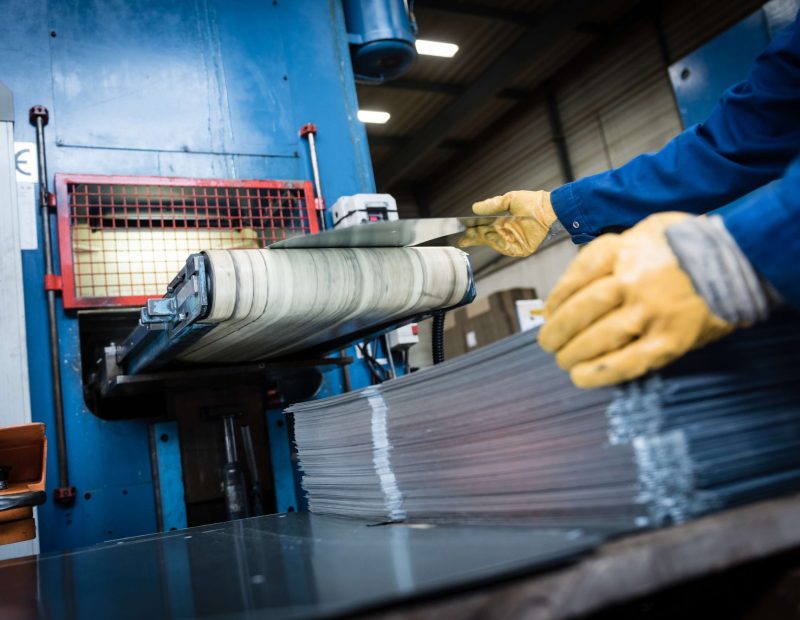
Part 3: Strategic Considerations and Environmental Impact
3.1 Maintenance and Durability for Stable Productivity
Press tools, thanks to their robustness, require minimal maintenance, whereas punching and panel bending machines demand frequent adjustments. Establishing a preventive maintenance schedule increases equipment longevity and ensures smooth production.
3.2 Environmental Impact and Material Optimization
Modern equipment, like automated presses, reduces material waste through precision cutting. Optimized workflows cut metal scrap by up to 30%, lowering the carbon footprint while saving raw material costs for companies committed to eco-responsibility.
3.3 Lifespan and Recyclability of Equipment
Press tools, built for longevity, reduce the need for frequent replacements. Their recyclability supports a circular economy, and some manufacturers offer refurbishment options to extend their lifespan. Explore Ouréval’s sustainable and customized solutions for controlled ecological impact and consistent quality.
3.4 Energy Cost Comparison and Environmental Impact
Each machine has a different energy footprint. For instance, automatic presses, due to their speed, consume less energy per unit produced. In contrast, punching and panel bending machines require higher energy consumption due to frequent adjustments. Comparing these costs helps businesses align with their sustainability goals.
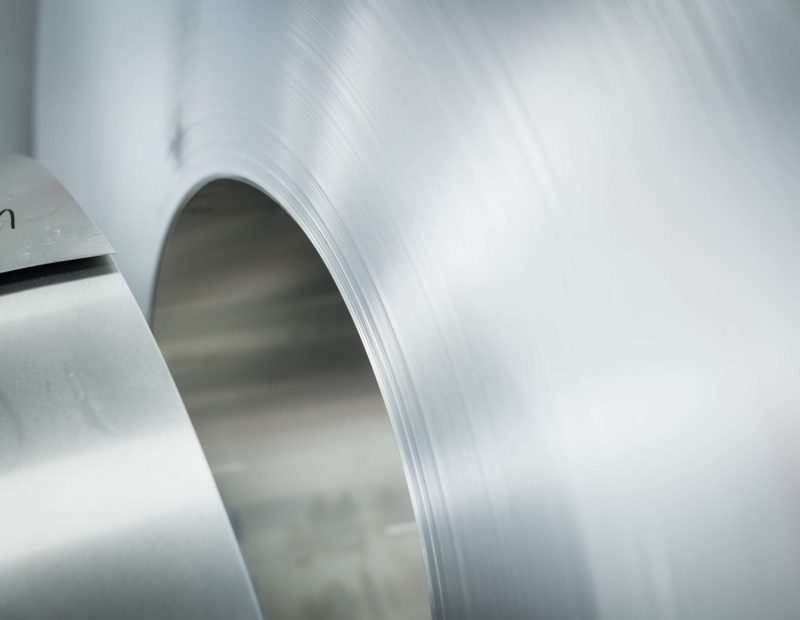
Conclusion: Choosing the Optimal Equipment for Your Production Needs
The choice between press tools, punching machines, and panel bending machines depends on production goals and sustainability requirements. For large-scale runs demanding uniform quality, press tools are the most cost-effective. For customized production, punching and panel bending machines provide the required flexibility.
Contact our industrial tooling experts for a personalized consultation and learn how these solutions can transform your production while addressing current environmental challenges.
A certified quality partner
for the overall management of your projects
Comprehensive solution
From the prototype to the delivery of series parts to the client
Tailored production
Medium and large series
50 years of experience
30 people at your service - recognised know-how and expertise
Certified quality
Certification according to ISO 9001 and IATF 16949