Press Tooling refers to precision mechanical constructions used to perform forming operations on metal or plastic parts. Each tool consists of an upper movable part clamped to the slide and a lower fixed part, usually clamped to the press table. In this article, a technical definition of press tooling will be provided, along with examples of its uses and numerous advantages. Finally, you will discover the processes involved in creating a quality press tool.
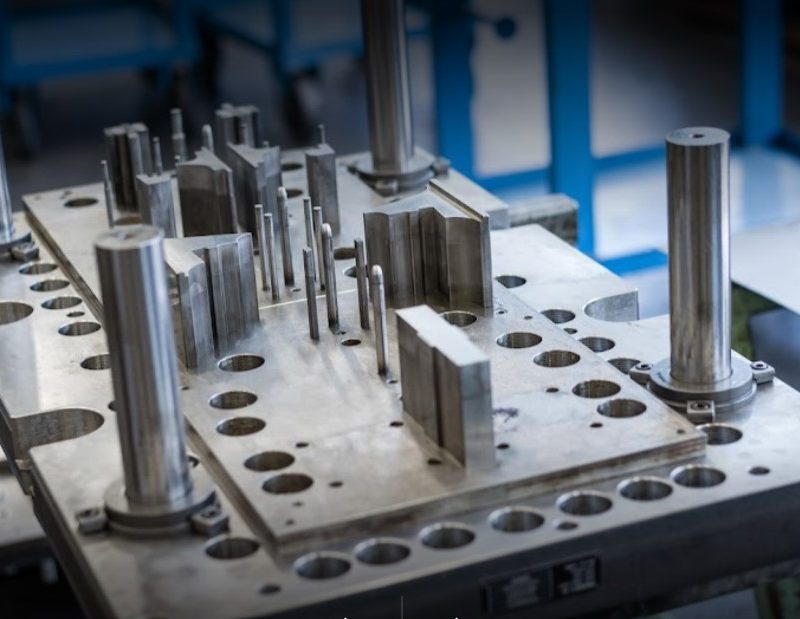
PRESS TOOLING : DEFINITION
What is a press tool?
Press tools are equipment used in the metalworking industry to form, bend, cut, stamp, or perforate metal parts. They are often molds or dies specifically designed to operate with mechanical or hydraulic presses.
Press tools generally consist of two main parts: the upper part called the “punch” and the lower part called the “die.” When a metal piece is placed between these two parts and the press is activated, the piece is shaped, cut, or stamped according to the tool’s form.
Press tools can be used in various industries. They are often custom-designed to meet the specific needs of each company.
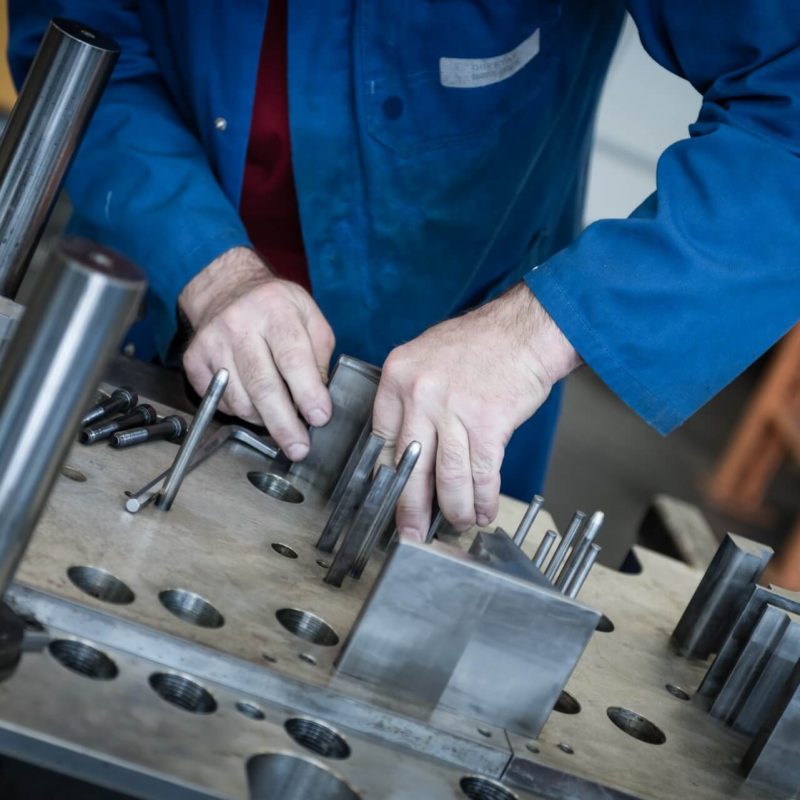
What are the uses of press tools?
Press tools are used in various industries that work with metal materials. Here are some examples of industries that use press tools:
- Automotive Industry: Press tools are used to manufacture automotive parts such as doors, hoods, fenders, bumpers, door frames, etc.
- Aerospace Industry: Press tools are used to manufacture aerospace parts such as wings, fuselages, landing gears, engines, etc.
- Electronics Industry: Press tools are used to manufacture electronic parts such as component enclosures, connectors, heat sinks, etc.
- Construction Industry: Press tools are used to manufacture steel parts such as beams, columns, angles, C-profiles, etc.
- Furniture Manufacturing Industry: Press tools are used to manufacture furniture parts in steel or aluminum such as table legs, chair supports, hinges, etc.
In short, any company that works with metals and needs to shape them precisely and repeatedly can use press tools to manufacture parts according to required specifications.
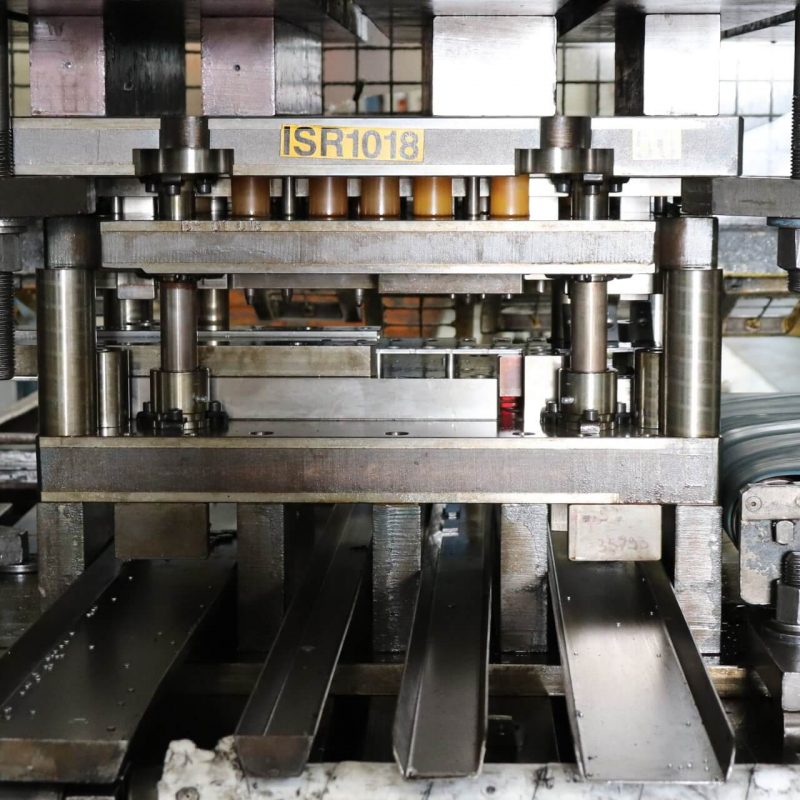
What are the advantages of press tools?
Press tools offer several advantages for companies that use them. Here are a few:
- Precision: Press tools allow the production of metal parts with high precision, reducing errors and waste.
- Speed: Press tools are designed to work at high speed, enabling the production of large quantities of parts in a short time.
- Consistency: Press tools ensure regular and homogeneous production, which is particularly important for industries that need identical parts to assemble their products.
- Cost-effectiveness: Press tools are often used to produce parts in large quantities, reducing the cost per unit.
- Flexibility: Press tools can be designed to produce a wide variety of parts, allowing companies to quickly adapt to market needs.
In summary, press tools increase production efficiency, reduce costs, improve part quality, and adapt to rapid market changes.
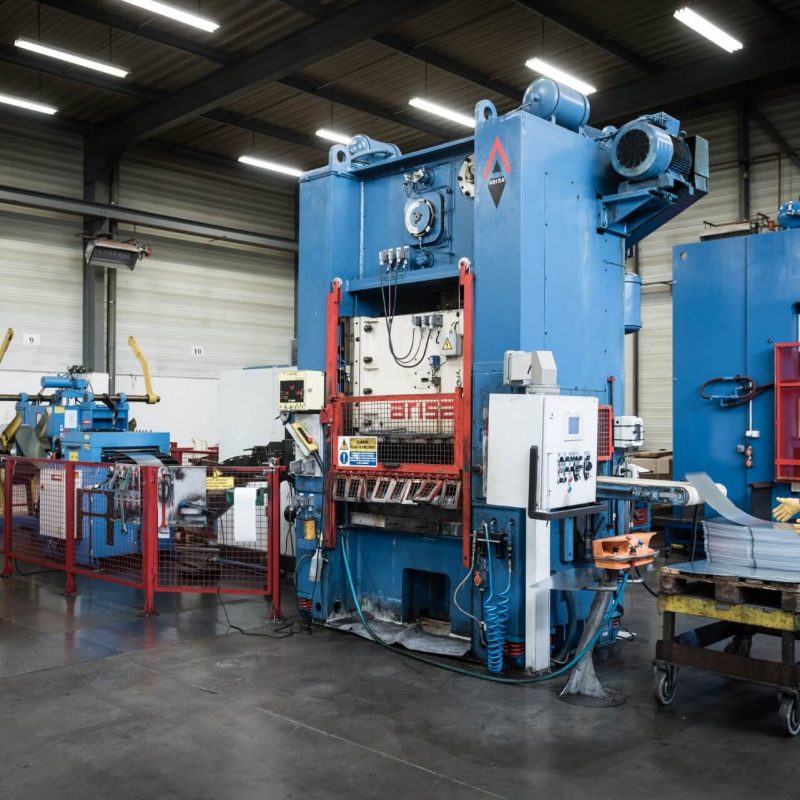
MANUFACTURING A PRESS TOOL
The manufacturing of press tools can be done by several processes depending on the design requirements and materials used. Here are some of the most common processes:
Machining
Machining is a manufacturing process that involves removing material from a raw piece to achieve precise shapes and dimensions. This process can be carried out using a variety of machine tools such as lathes, milling machines, drills, and grinders.
When the raw piece is placed in the machine tool, cutting tools are used to remove chips from the piece. The cutting tools can be drills, milling cutters, taps, reamers, etc. These tools are usually made of high-speed steel or tungsten carbide and are highly wear-resistant. The machine tools used for machining are equipped with numerical control devices (CNC) that allow the machine to be programmed to perform machining operations with high precision.
Machining can be used to produce a wide variety of tool parts such as punches, dies, and other tool components. Machining is also used to manufacture high-precision parts for industries such as aerospace, defense, medicine, and automotive.
In summary, machining is a manufacturing process that involves removing material from a raw piece using cutting tools to achieve precise shapes and dimensions. It is a very common manufacturing technique in the industry that allows the production of a wide variety of parts with high precision and reliability. However, to achieve optimal results, it is important to have a good understanding of the properties of the materials used for machining, such as hardness and ductility, and to choose the appropriate machining tools for the shape and size of the piece to be machined.
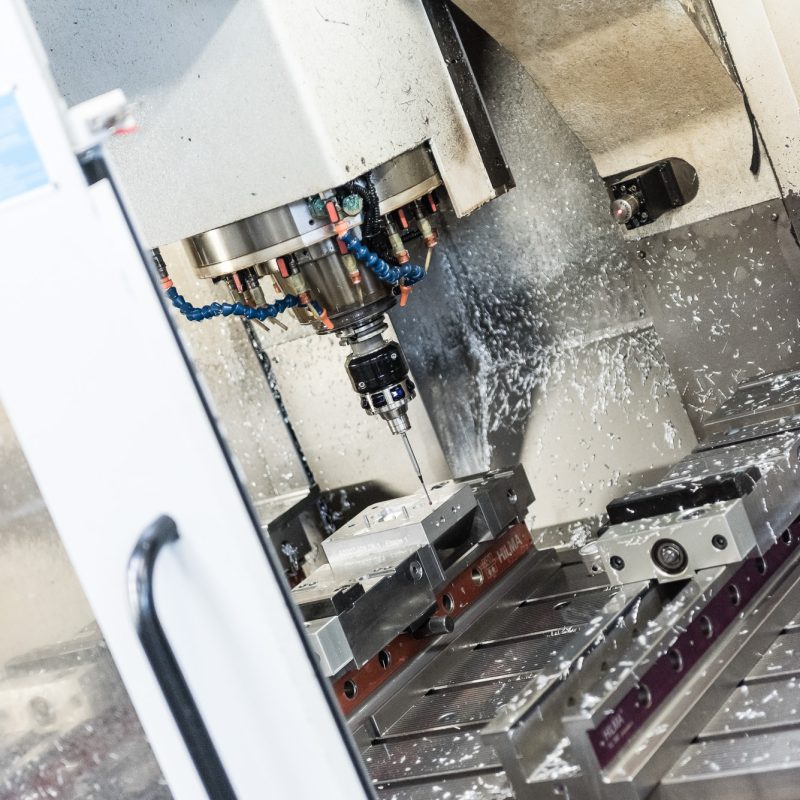
Electrical Discharge Machining (EDM)
EDM is a manufacturing process that uses electrical discharges to remove material from a workpiece. In the context of making press tools, EDM can be used to produce tool parts with high precision and a high-quality surface finish.
EDM can be done by sinking. In this case, it involves using a copper or graphite electrode held at a small distance from the workpiece. Alternatively, wire EDM uses the electrical erosion of the material with a conductive wire.
When the electrode or wire is connected to a power supply and comes into contact with the piece, a spark is generated, producing enough heat to melt and vaporize a small amount of material. The debris is then removed by a dielectric fluid such as oil or water sprayed onto the work area.
The EDM process can be used to produce complex-shaped tool parts such as cavities and cooling channels that would be difficult or impossible to achieve with other machining methods. EDM is also useful for machining hard and brittle materials such as titanium alloys and ceramics.
EDM is an expensive and slow manufacturing process but allows the production of tool parts with high precision and a high surface quality. However, to achieve optimal results, it is important to have a good understanding of the properties of the materials used for EDM and to choose the appropriate process parameters for the shape and size of the workpiece.
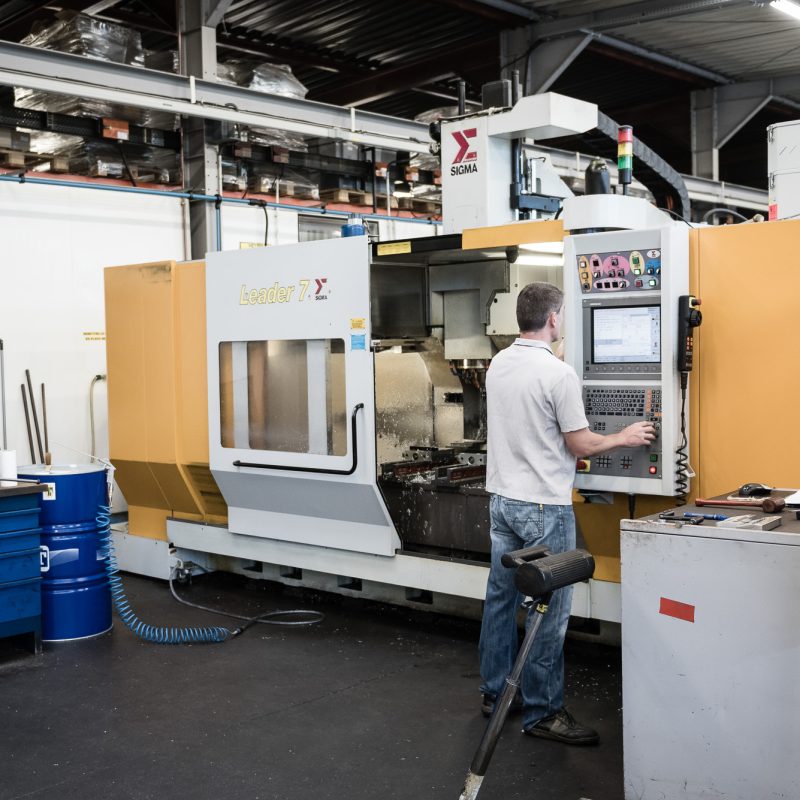
Grinding
Grinding involves using an abrasive wheel to remove thin layers of material from a workpiece to achieve precise dimensions and a high-quality surface. In the context of making press tools, grinding is often used to produce tool parts with high dimensional precision and a high-quality surface finish.
The grinding process involves using an abrasive wheel, which can be made of various materials such as corundum, silicon carbide, diamond, or CBN. The wheel is rotated at a high speed and applied to the workpiece, resulting in material removal by abrasion. The shape of the wheel determines the shape of the produced part.
Grinding can be used to produce tool parts of various shapes such as punches, dies, and spindles. Parts produced by grinding can be machined with high dimensional precision, allowing precise fits between tool parts. Grinding also allows achieving a high-quality surface finish, which can improve tool life and reduce production costs.
Grinding is an expensive and relatively slow manufacturing process but allows the production of tool parts with high precision and a high-quality surface. However, to achieve optimal results, it is important to choose the appropriate wheel material for the properties of the workpiece material and select the appropriate process parameters such as wheel rotation speed, application pressure, and feed rate.
In summary, the manufacturing of press tools can be done by various processes depending on design requirements and materials used. Toolmakers must choose the appropriate process based on tool complexity, required precision, material hardness, and manufacturing time and costs.
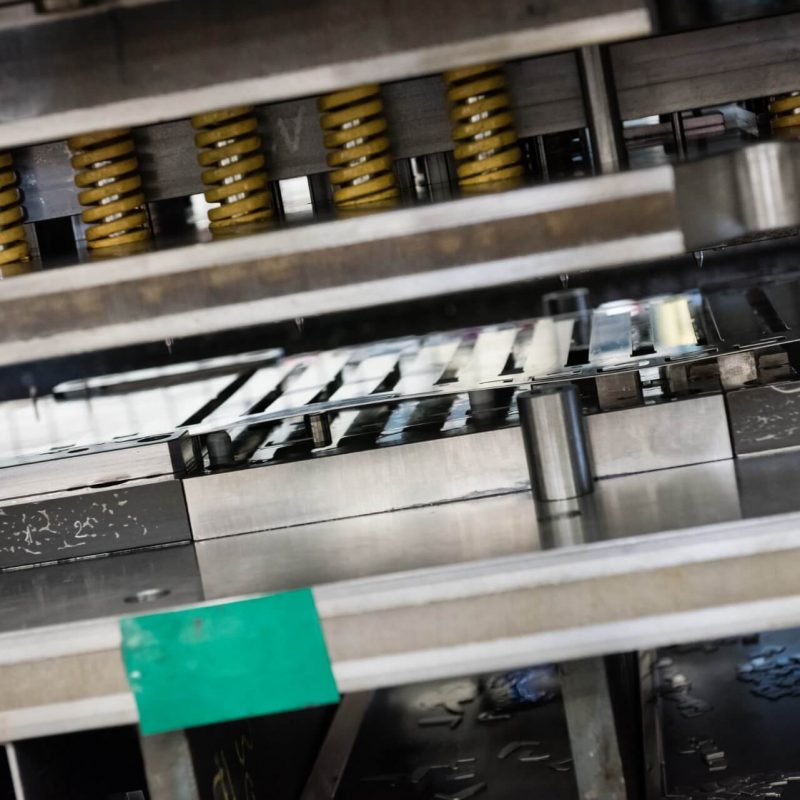
Trusted Partner in Press Tool Manufacturing
Companies that manufacture press tools must possess technical skills, flexibility, responsiveness, production capabilities, innovation, and after-sales service to be competitive and meet market needs.
Since 1973, Ouréval has been putting its expertise at the service of its clients in the design and production of custom press tools. This Alsatian company offers a comprehensive service from co-development to the final manufacture of press tools and their use on the press.
Ouréval is a trusted partner that offers many advantages:
- Technical skills: Ouréval has over 50 years of technical expertise in the design, manufacture, and maintenance of press tooling to ensure their quality and durability.
- Flexibility: Ouréval can design and produce press tools for a wide variety of metal parts while being able to quickly adapt to changing market demands.
- Responsiveness: Meeting deadlines and managing emergencies is a priority for the Alsatian company. Every effort is made to meet customer requirements as quickly as possible.
- Production capacities: Ouréval has significant production capacities to meet clients’ needs in terms of quantity and delivery times. Their machine park is varied with presses ranging from 25 to 400 tons.
- Innovation: Ouréval designs innovative and efficient press tools using advanced technologies to improve quality, competitiveness, and production precision.
- Quality: Press tools are manufactured according to strict quality standards to ensure their reliability and durability. Ouréval implemented an ambitious and effective quality approach very early on. They were among the first in Europe to adopt a quality management system compliant with the automotive standard IATF16949 in addition to ISO 9001.
- After-sales service: Ouréval provides high-quality after-sales service to ensure the maintenance, repair, and replacement of press tools if necessary.
For more information regarding the design and manufacture of press tools, feel free to contact the Ouréval team.
A certified quality partner
for the overall management of your projects
Comprehensive solution
From the prototype to the delivery of series parts to the client
Tailored production
Medium and large series
50 years of experience
30 people at your service - recognised know-how and expertise
Certified quality
Certification according to ISO 9001 and IATF 16949