Metal stamping and cutting is a manufacturing process that involves deforming or cutting raw sheet metal by applying pressure using a numerically controlled press with specific tools. This article will comprehensively explain this process. We will also highlight its advantages and applications. Finally, we will offer advice on choosing a quality metal stamping service provider.
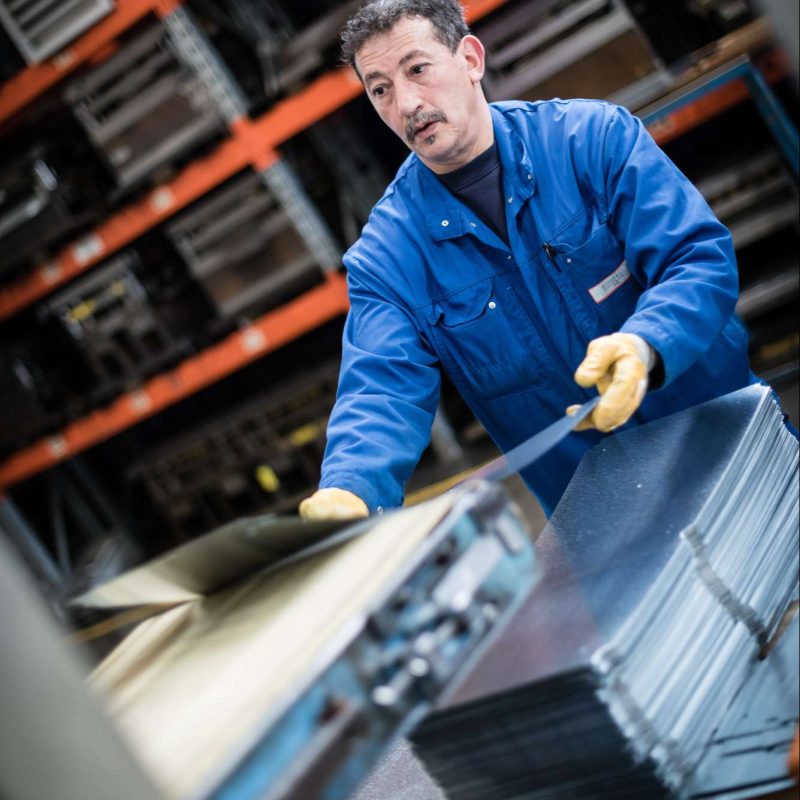
EXPLAINING METAL STAMPING AND CUTTING FROM A TO Z
Definition of Metal Stamping and Cutting
Metal stamping and cutting is a manufacturing technique that involves cutting a metal sheet into a predefined shape using a tool called a press. This operation creates a raw piece that is then formed using another press equipped with a stamping tool.
The stamping process involves applying force to the metal sheet to deform, bend, or pierce it according to design specifications. The goal is to create a piece with precise shape and dimensions.
Metal stamping and cutting is commonly used in the automotive industry for manufacturing parts such as doors, engine hoods, fenders, gas tank caps, gearboxes, etc. It is also used in the aerospace industry, household appliance manufacturing, and many other manufacturing sectors.
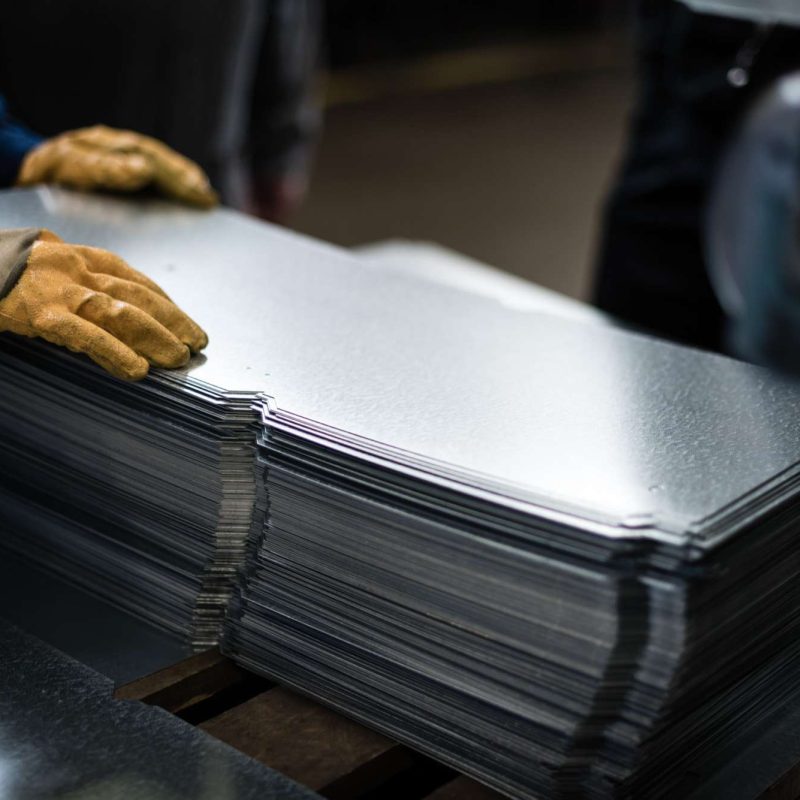
Raw Materials Used in Metal Stamping and Cutting
Metal stamping and cutting can be performed on various materials, including metals and alloys. The most commonly used raw materials in metal stamping and cutting are:
- Steel: This is the most commonly used material in the automotive industry for manufacturing body parts such as doors, engine hoods, fenders, etc. Different types of steel exist, each with specific mechanical properties suitable for specific applications.
- Aluminum: Widely used in the aerospace industry for manufacturing lightweight structural parts such as wings, fuselages, landing gears, etc. It is also used in the automotive industry for suspension components and transmission housings.
- Copper Alloys: Used for manufacturing electronic and electrical parts, including connectors, relays, transformers, etc.
- Titanium Alloys: Used in the aerospace industry for manufacturing corrosion-resistant and high-temperature-resistant structural parts like aircraft engine components.
It is important to note that different raw materials have varying properties and require specific stamping and cutting techniques to achieve the desired pieces.
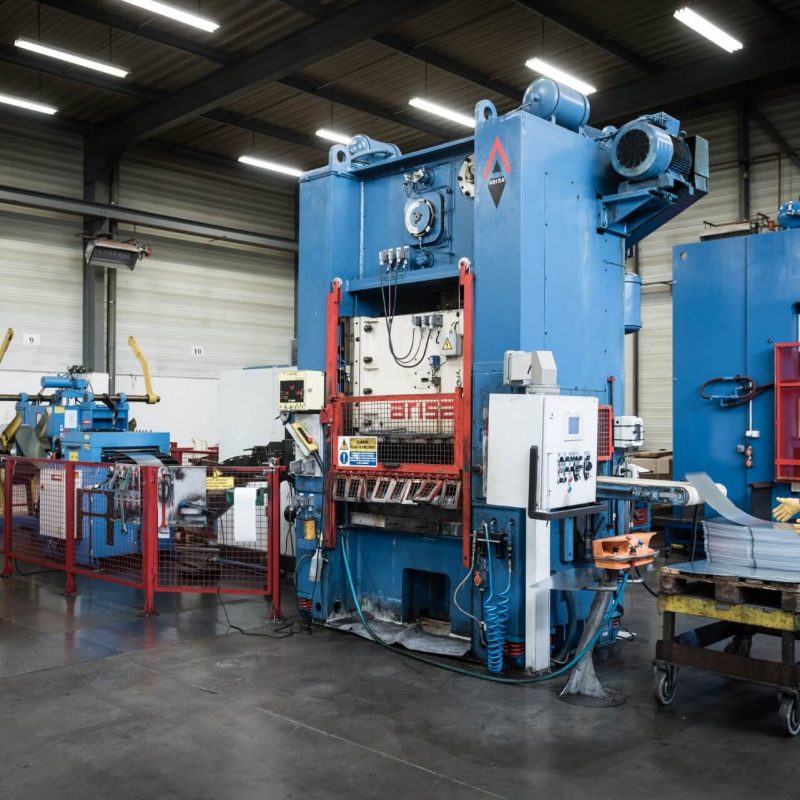
Advantages of Metal Stamping and Cutting
Metal stamping and cutting offer several advantages, including:
- Increased Productivity: This is a highly automated process, allowing for rapid production of large quantities of parts with high precision and repeatability.
- Cost Reduction: The process is cost-effective as it enables the production of large quantities of parts at a lower cost per unit.
- High Flexibility: This manufacturing technique is highly flexible and can be used to produce a wide variety of parts with different shapes, dimensions, and thicknesses.
- High Dimensional Precision: Allows for the production of parts with high dimensional precision, essential for components that must be assembled with other parts.
- Waste Reduction: Due to its high precision, it minimizes raw material waste, reducing production costs.
- High Surface Quality: Can produce parts with a smooth and uniform surface, reducing finishing costs and improving the aesthetic quality of finished products.
In summary, metal stamping and cutting is an efficient and flexible process that allows for the production of high-quality parts in large quantities at a lower cost.
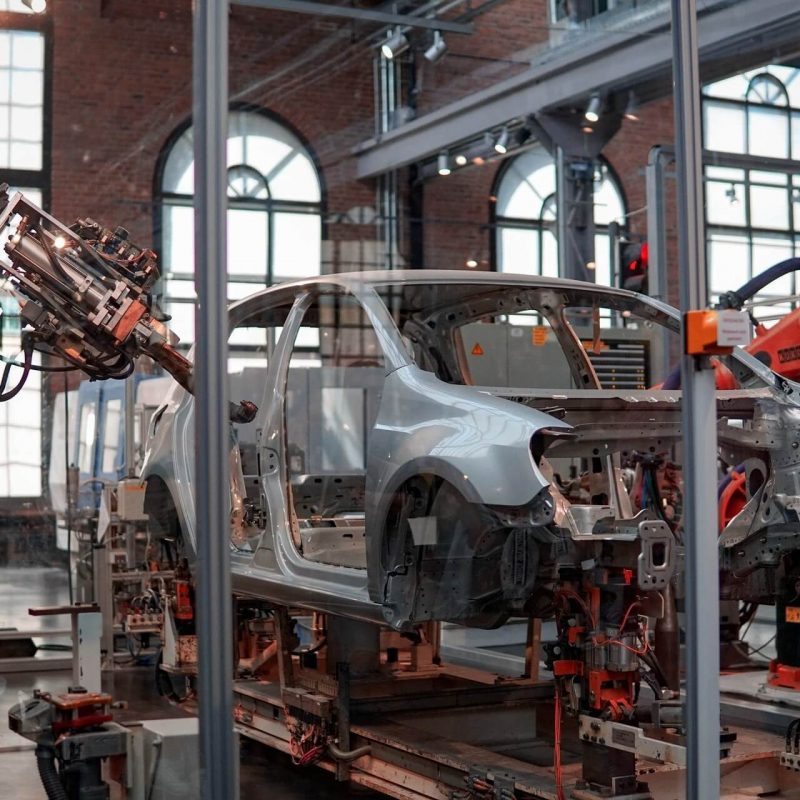
Applications of Metal Stamping and Cutting
Metal stamping and cutting is a commonly used manufacturing technique in various industrial sectors, including:
- Automotive Industry: Used for producing body parts such as doors, fenders, engine hoods, bumpers, etc. It is also used for manufacturing suspension components, gearboxes, and other structural parts.
- Aerospace Industry: Used for manufacturing structural parts for aircraft such as wings, fuselages, landing gears, etc.
- Household Appliance Industry: Used for producing parts for appliances like washing machines, dryers, refrigerators, etc.
- Electronics Industry: Used for manufacturing connectors, component housings for printed circuit boards, etc.
- Medical Industry: Used for manufacturing parts for medical equipment such as drug delivery devices, surgical tools, etc.
- Construction Industry: Used for manufacturing construction parts such as steel structural components and roofing elements.
In summary, metal stamping and cutting is used in a wide variety of industrial sectors to produce high-quality parts in large quantities at a lower cost.
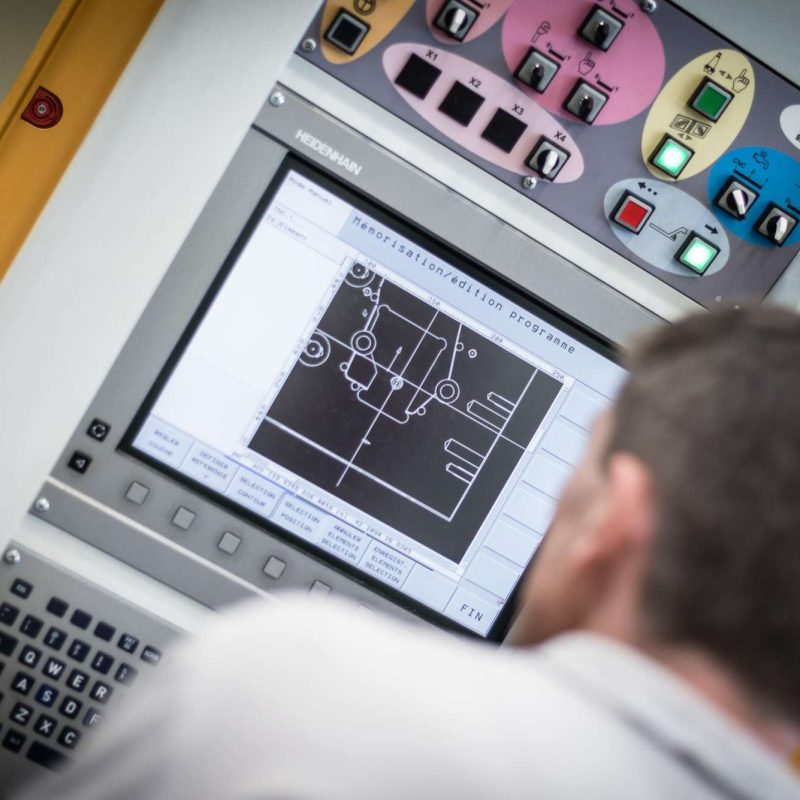
Steps in the Metal Stamping and Cutting Process
The metal stamping and cutting process generally includes several steps such as:
- Tooling Design: The first step involves designing the tool’s shape and dimensions according to client specifications.
- Tool Manufacturing: Once the part design is finalized, the stamping tool must be manufactured. The tool is usually made from a steel block or similar material and may include several elements such as dies, punches, etc.
- Raw Material Preparation: The raw material used for the process is usually a coil of steel, aluminum, or stainless steel sheet. The coil is unrolled and cut to the required size for the part to be stamped.
- Part Cutting: The first step involves cutting the part from the metal sheet using a punch and die. The punch cuts the part from the sheet while the die holds the sheet in place.
- Stamping: Once the part is cut, it is placed in a stamping press that applies force to shape it. This step can be done in one or multiple stages depending on the complexity of the shape.
- Finishing: Once stamped, the part may require additional finishing to remove burrs and imperfections. This can be done using tools such as grinders or milling machines.
- Inspection: Finally, the part is inspected to ensure it meets client specifications in terms of shape, dimensions, and surface quality. Parts that do not meet quality standards are rejected.
In summary, the metal stamping and cutting process includes several important steps from part design to the final inspection of the stamped part.
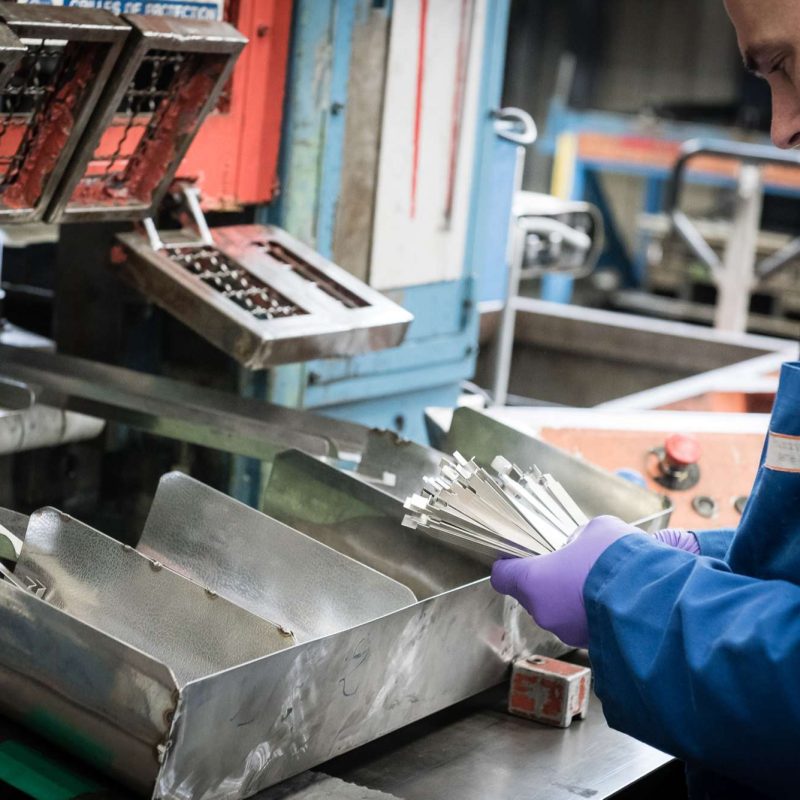
Alternatives to Metal Stamping and Cutting
There are several alternatives to metal stamping and cutting, including:
- Machining: A process that uses tools to remove raw material and shape the part. Often used for high-precision metal parts manufacturing but is more expensive than metal stamping and cutting.
- Additive Manufacturing: Also known as 3D printing, this process creates parts by adding material layer by layer. Ideal for manufacturing complex and customized parts but slower than metal stamping and cutting, and the surface quality may be inferior.
- Forming: A material shaping process without material removal. Often used for plastic parts manufacturing but can also be used for metals. Less expensive than machining but may require costly tools for each shape.
- Laser Cutting: A process that uses a laser beam to cut parts from raw material. Precise and can be used for cutting metals and non-metallic materials but is more expensive than metal stamping and cutting.
In summary, there are several alternatives to metal stamping and cutting, each with its advantages and disadvantages. The choice of manufacturing process will depend on part specifications, the required quantity, and the available budget.
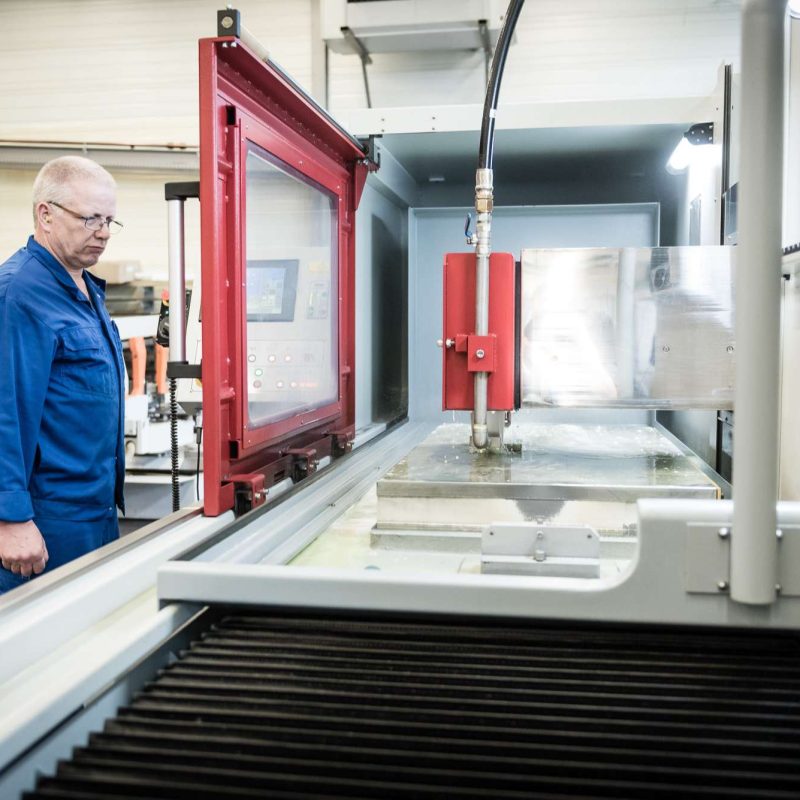
METAL STAMPING AND CUTTING: HOW TO CHOOSE YOUR SERVICE PROVIDER?
Elements to Consider When Choosing a Provider
Choosing a provider for metal stamping and cutting is crucial to ensure part quality and client satisfaction. Here are some criteria to consider:
- Technical Competence: The provider must have the technical skills necessary for metal stamping and cutting. Check their experience in the field, certifications, and client references.
- Production Capacity: Ensure that the provider has the production capacity to meet your needs in terms of quantity and lead time. Check the number of stamping presses they have, the size of their production team, etc.
- Quality: The provider must guarantee the quality of the stamped part. Request to see samples of previously produced parts and check the finishing quality, adherence to dimensional tolerances, etc.
- Cost: Cost is an important factor when choosing a provider. Request quotes from several providers to compare prices and ensure costs are transparent with no hidden fees.
- Customer Service: Ensure the provider is available to answer your questions and concerns. They should be responsive and able to provide regular updates on your project’s progress.
- Location: The provider’s location can also be a deciding factor. It is often preferable to choose a provider close to your business to facilitate communication and reduce transportation costs.
In summary, to choose the right provider for metal stamping and cutting, it is important to consider several criteria such as technical competence, production capacity, quality, cost, customer service, and location. It is also recommended to ask for client references and check the provider’s reputation before making a final decision.
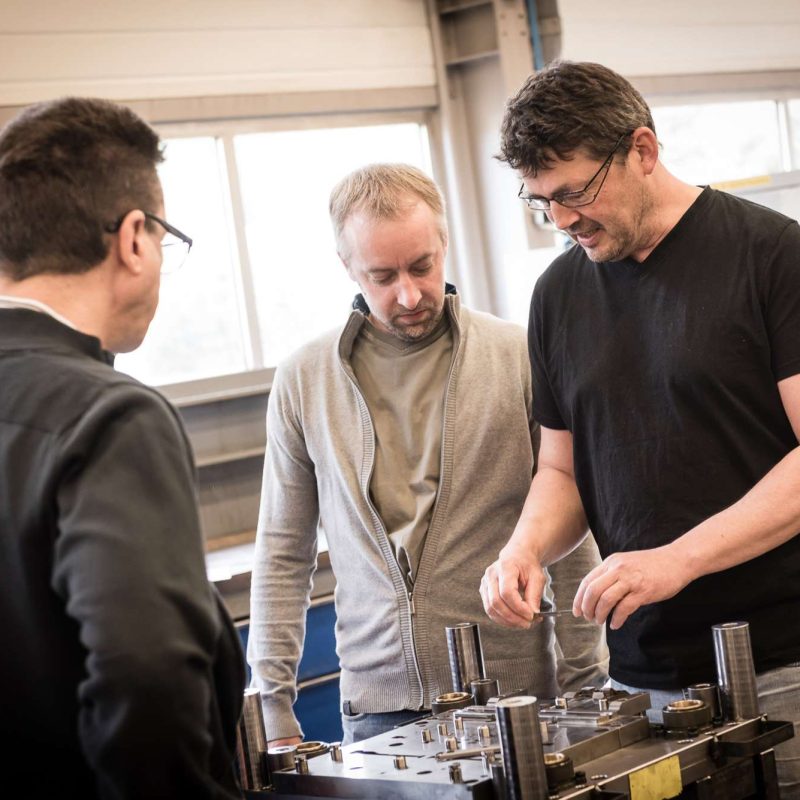
Ouréval: Over 50 Years of Expertise in Metal Stamping and Cutting
For more than 50 years, Ouréval has specialized in transforming raw sheet metal for the production of medium and large series metal parts. We offer metal stamping and cutting solutions using automatic presses.
Ouréval uses numerically controlled automatic presses to perform the stamping and cutting of metal parts. This technique involves deforming or cutting the sheet metal by applying pressure with a progressive die, allowing the production of complex-shaped parts.
This process is ideal for medium and large series manufacturing and is widely used in the automotive industry for its precision, execution quality, and competitive cost. If our clients have their own tools, we can also perform stamping and cutting after validating their feasibility and compatibility with our presses.
Our method allows us to transform various materials such as steel, aluminum, stainless steel, and coated sheet metal (galvanized, electro-galvanized, pre-painted). We can process sheet thicknesses ranging from 0.5 to 6 mm and work with metal coils up to 660 mm wide.
Feel free to contact the Ouréval team and our design office if you would like more information about metal stamping and cutting.
A certified quality partner
for the overall management of your projects
Comprehensive solution
From the prototype to the delivery of series parts to the client
Tailored production
Medium and large series
50 years of experience
30 people at your service - recognised know-how and expertise
Certified quality
Certification according to ISO 9001 and IATF 16949